Table of Contents
Top 15 Future Trends In Fluid Transfer Technology
Fluid transfer technology plays a crucial role in various industries, including manufacturing, healthcare, energy, and more. As technology continues to evolve, so does the field of fluid transfer. In this article, we will explore the top 15 future trends in fluid transfer technology that are expected to shape the industry in the coming years.
1. Smart Fluid Transfer Systems:
Smart Fluid Transfer Systems represent a revolutionary advancement in fluid handling technology. As industries continue to embrace automation and connectivity, the integration of smart technologies into fluid transfer systems is poised to bring about significant improvements in efficiency, reliability, and overall performance. Here, we delve deeper into the concept of Smart Fluid Transfer Systems and the key elements driving this trend.
Key Components of Smart Fluid Transfer Systems:
Sensors and Actuators:
Smart fluid transfer systems are equipped with an array of sensors that monitor various parameters such as pressure, flow rate, temperature, and fluid quality. These sensors provide real-time data, enabling precise control and immediate response to any deviations from optimal operating conditions. Actuators, on the other hand, facilitate automated adjustments based on the information gathered by sensors.
Data Analytics and Machine Learning:
The collected data from sensors is analyzed using advanced algorithms and machine learning techniques. This allows the system to identify patterns, predict potential issues, and optimize performance over time. Machine learning algorithms can adapt to changing conditions, improving the efficiency and reliability of fluid transfer processes.
IoT Connectivity:
Smart fluid transfer systems are an integral part of the Internet of Things (IoT). They are equipped with connectivity features that enable seamless communication with other devices, centralized control systems, and cloud-based platforms. This connectivity allows for remote monitoring, data storage, and real-time decision-making.
Human-Machine Interface (HMI):
An intuitive HMI provides a user-friendly interface for operators and maintenance personnel. It allows for easy monitoring of system parameters, diagnostics, and control adjustments. In some cases, augmented reality (AR) interfaces may be employed for more immersive and interactive user experiences.
Predictive Maintenance:
Smart fluid transfer systems can predict maintenance needs based on the data collected from sensors and historical performance. This proactive approach minimizes downtime by allowing for scheduled maintenance activities, preventing unexpected failures, and reducing overall maintenance costs.
Advantages of Smart Fluid Transfer Systems:
Efficiency Optimization:
Real-time monitoring and control enable the system to adjust parameters dynamically, optimizing fluid transfer processes for maximum efficiency. This can result in energy savings, reduced waste, and improved overall productivity.
Enhanced Safety:
Smart systems can promptly detect anomalies, leaks, or other safety concerns. Automated responses or alerts ensure a swift reaction to potential hazards, minimizing the risk of accidents and enhancing overall workplace safety.
Remote Accessibility:
The IoT connectivity of smart fluid transfer systems allows for remote access and control. Operators and maintenance teams can monitor and manage systems from anywhere, facilitating quick responses to issues without the need for physical presence.
Cost Reduction:
Predictive maintenance and optimized operations contribute to cost reduction by minimizing downtime, extending equipment lifespan, and reducing energy consumption. The efficient use of resources also leads to lower operational costs.
Environmental Sustainability:
Smart fluid transfer systems can contribute to environmental sustainability by optimizing resource usage, reducing waste, and supporting the adoption of greener fluid transfer solutions. This aligns with the global shift toward eco-friendly industrial practices.
2. Nanotechnology in Fluid Transfer:
Nanotechnology is rapidly becoming a game-changer in various industries, and its application in fluid transfer technology holds tremendous potential. Nanotechnology involves manipulating materials at the nanoscale, typically at dimensions less than 100 nanometers. In the context of fluid transfer, nanotechnology brings forth a range of innovations that enhance performance, durability, and efficiency. Here, we delve into the implications and advancements of nanotechnology in fluid transfer systems.
1. Advanced Materials:
Nanotechnology allows for the creation of advanced materials with nanostructured features. Nanocomposites, which incorporate nanoparticles into traditional materials, enhance the mechanical properties, corrosion resistance, and durability of components used in fluid transfer systems.
2. Improved Lubrication:
Nanoparticles, such as graphene or nanodiamonds, can be used as additives in lubricants. The introduction of nanoscale lubricants improves the efficiency of fluid transfer systems by reducing friction and wear, leading to longer component lifespan and increased energy efficiency.
3. Anti-fouling Surfaces:
Nanocoatings with anti-fouling properties can be applied to the surfaces of pipes, tubes, and other fluid transfer components. These coatings prevent the accumulation of contaminants, reducing the likelihood of clogs, blockages, and the need for frequent maintenance.
4. Nanostructured Filters:
Nanotechnology enables the design and manufacturing of highly efficient nanostructured filters. These filters can selectively remove particles and contaminants from fluids, ensuring a higher level of purity in the transferred substances. This is particularly critical in industries such as pharmaceuticals and food processing.
5. Responsive Nanomaterials:
The development of smart and responsive nanomaterials allows for the creation of components that can adapt to changing conditions. For instance, nanomaterials that respond to temperature, pressure, or chemical changes can enhance the controllability and adaptability of fluid transfer systems.
6. Nanoscale Sensors:
Nanosensors embedded in fluid transfer systems can provide real-time monitoring of various parameters, including pressure, temperature, and fluid composition. These sensors enable precise control and contribute to the overall efficiency and safety of fluid transfer processes.
7. Reduced Friction Losses:
Nanofluids, which are liquids containing suspended nanoparticles, exhibit unique flow properties. The addition of nanoparticles to fluids can reduce friction losses in pipes, resulting in improved flow rates and energy savings in fluid transfer systems.
8. Self-healing Materials:
Nanotechnology facilitates the development of self-healing materials that can repair damage at the nanoscale. In fluid transfer systems, this innovation can contribute to increased resilience and reduced susceptibility to leaks or structural failures.
9. Miniaturization of Components:
Nanotechnology allows for the miniaturization of components in fluid transfer systems. This is particularly advantageous in applications where space is limited, such as medical devices or microfluidic systems.
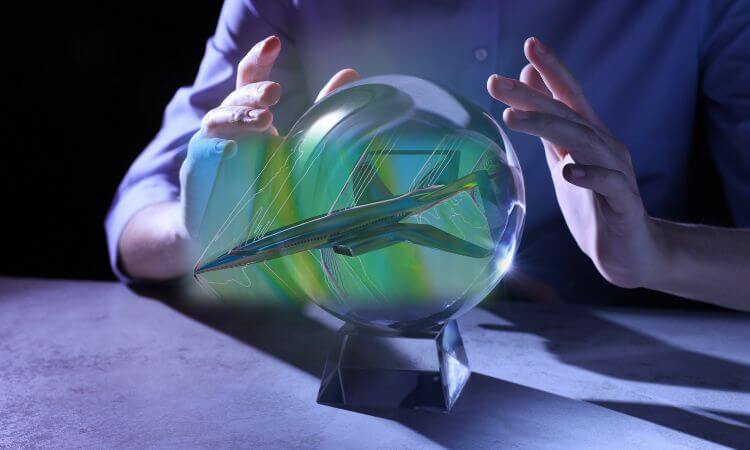
Future Outlook and Challenges:
As nanotechnology continues to advance, the future of fluid transfer systems will likely see even more groundbreaking developments. However, challenges such as cost, scalability, and potential environmental impact need to be addressed. Additionally, the responsible and ethical use of nanomaterials must be considered to ensure safety and regulatory compliance.
In conclusion, nanotechnology is transforming the landscape of fluid transfer technology by introducing novel materials and design concepts. As research and development in this field progress, nanotechnology is expected to play a pivotal role in creating more efficient, durable, and environmentally friendly fluid transfer systems across various industries.
3. 3D Printing for Customized Components:
3D printing, also known as additive manufacturing, has emerged as a revolutionary technology with wide-ranging applications across various industries. One of the exciting areas where 3D printing is making a significant impact is in the production of customized components for fluid transfer systems. This article explores how 3D printing is transforming the manufacturing process, allowing for the creation of bespoke components tailored to specific requirements within fluid transfer technology.
1. Customized Designs:
3D printing enables the production of complex and intricate designs that would be challenging or impossible with traditional manufacturing methods. This level of customization is particularly advantageous in fluid transfer systems where components often need to conform to unique spatial constraints and performance specifications.
2. Optimized Fluid Flow:
Traditional manufacturing techniques may have limitations in creating components with precisely engineered internal geometries. 3D printing allows for the design and production of fluid transfer components with optimized internal structures, leading to improved fluid flow characteristics and reduced pressure losses.
3. Material Variety:
3D printing supports a wide range of materials, including polymers, metals, ceramics, and composites. This versatility allows manufacturers to choose materials that best suit the specific requirements of fluid transfer components, considering factors such as chemical resistance, strength, and durability.
4. Rapid Prototyping:
The iterative nature of 3D printing facilitates rapid prototyping. Design modifications can be quickly implemented, and prototypes can be produced in a matter of hours. This accelerates the product development cycle, enabling engineers to test and refine fluid transfer components more efficiently.
5. Reduced Waste:
Traditional subtractive manufacturing methods often result in material wastage during the machining process. 3D printing, being an additive process, minimizes material wastage, contributing to more sustainable manufacturing practices.
6. On-Demand Production:
3D printing allows for on-demand and localized production of components. This is particularly advantageous for fluid transfer systems where specific components may be needed urgently or in low quantities. It reduces lead times and eliminates the need for large inventories.
7. Complex Cooling Channels:
In industries such as automotive and aerospace, 3D printing is used to create components with intricate cooling channels. This concept can be applied to fluid transfer systems, where components with embedded channels for temperature regulation can be produced, enhancing efficiency in heat exchange processes.
8. Integration of Multiple Components:
3D printing facilitates the creation of complex, integrated assemblies in a single production step. This capability allows for the consolidation of multiple components into a single, seamless structure, reducing assembly requirements and potential points of failure.
9. Lightweight Structures:
The design freedom offered by 3D printing allows for the creation of lightweight structures without compromising strength. In fluid transfer systems, this can lead to reduced overall weight and improved energy efficiency.
4. Wireless Connectivity and IoT Integration:
Wireless connectivity and Internet of Things (IoT) integration have become integral components in the evolution of fluid transfer technology. These advancements offer a paradigm shift in how fluid transfer systems are monitored, controlled, and optimized. In this article, we explore the impact of wireless connectivity and IoT integration on fluid transfer systems, highlighting the benefits and future implications of this transformative trend.
1. Real-Time Monitoring and Control:
Wireless sensors embedded in fluid transfer systems enable real-time monitoring of key parameters such as pressure, flow rate, temperature, and fluid quality. This data is transmitted wirelessly, providing operators with immediate insights into system performance and allowing for prompt adjustments to optimize fluid transfer processes.
2. Remote Accessibility:
The integration of wireless connectivity allows for remote access to fluid transfer systems. Operators and maintenance personnel can monitor and control these systems from anywhere with an internet connection, improving overall operational efficiency and reducing the need for on-site presence.
3. Predictive Maintenance:
IoT-enabled fluid transfer systems can predict maintenance needs based on data collected from sensors. Predictive analytics and machine learning algorithms analyze historical performance data to anticipate potential issues, enabling scheduled maintenance and minimizing unplanned downtime.
4. Energy Efficiency:
Wireless connectivity facilitates the integration of smart energy management systems. By analyzing real-time data and historical trends, fluid transfer systems can be optimized for energy efficiency, contributing to reduced energy consumption and operational costs.
5. Data Analytics and Insights:
The vast amount of data generated by IoT-connected fluid transfer systems provides opportunities for in-depth analytics. Data analysis can uncover patterns, identify areas for improvement, and support data-driven decision-making for enhanced system performance.
6. Integration with Cloud Platforms:
IoT integration often involves cloud-based platforms where data is stored, processed, and analyzed. Cloud connectivity allows for centralized data management, scalability, and accessibility from various devices, fostering a more streamlined and collaborative approach to fluid transfer system management.
7. Enhanced Security Measures:
The integration of IoT in fluid transfer systems brings attention to cybersecurity. Advanced encryption and authentication protocols are essential to safeguard the wireless communication between devices and prevent unauthorized access or potential cyber threats.
8. Scalability and Flexibility:
Wireless connectivity and IoT integration offer scalable solutions. As fluid transfer systems evolve, additional sensors and devices can be easily integrated, providing flexibility to adapt to changing operational requirements.
9. Condition-Based Monitoring:
IoT-enabled sensors allow for condition-based monitoring of fluid transfer components. By continuously assessing the condition of pumps, valves, and other critical elements, the system can automatically trigger alerts or maintenance requests when abnormalities are detected.
5. Robotics in Fluid Handling:
Behold the audacious frontier of fluid handling, where the mundane shackles of tradition are obliterated, and the avant-garde spirit of robotics ushers in a revolutionary era. Brace yourself for a discourse that transcends the ordinary, shattering preconceived notions and demanding an unrestrained reimagining of the fluid transfer landscape.
1. Robo-Maestros of Fluid Choreography:
Picture this: a symphony of robotic virtuosos, each equipped with the finesse to navigate the intricate dance of fluid handling. These robotic marvels, akin to maestros, conduct a fluidic ballet with precision and grace, rendering human intervention an antiquated notion.
2. Automated Artistry:
Conventional fluid handling is a canvas, and robots are the artists injecting a newfound artistry. Imagine robotic appendages delicately manipulating valves, orchestrating pumps with algorithmic finesse, and choreographing fluidic movements that transcend the limits of human capability.
3. Machination Maestros:
Bid farewell to the mundane and embrace the rise of Machination Maestros – robotic virtuosos that redefine the orchestration of fluid dynamics. These ingenious contraptions not only handle fluids but elevate it to a performance, a symphony of automated prowess.
4. Fluidic Mavericks Unleashed:
Unshackle the fluidic mavericks – robots engineered to challenge conventions and disrupt the archaic norms of fluid handling. These fearless automatons navigate the complex terrains of pipes and conduits, redefining what was once deemed impossible with their unprecedented dexterity.
5. Automatons Defying Gravity:
Picture robotic wonders defying the laws of gravity as they traverse vertically and horizontally, effortlessly navigating the three-dimensional labyrinth of pipes. These automatons are not bound by earthly constraints, heralding a paradigm shift in fluid transfer possibilities.
6. Fluidic Ballet in Hazardous Terrains:
Send in the robotic prima donnas to perform a fluidic ballet in hazardous terrains, where human intervention poses risks. These mechanical virtuosos gracefully waltz through perilous environments, handling toxic substances and high-pressure flows with calculated ease.
7. Innovation Incarnate:
Robots are not just tools; they are the very embodiment of innovation. They represent a seismic shift in the narrative of fluid handling, where each robotic limb becomes a brushstroke on the canvas of progress, crafting an opus of efficiency and safety.
8. Liberate from Laborious Legacy:
Liberating industries from the laborious legacy of manual fluid handling, robots emerge as the liberators of efficiency. It’s time to bid adieu to the drudgery of routine tasks and embrace a future where robots tirelessly toil in the name of progress.
9. Fluidic Revolutionaries:
Robots aren’t mere assistants; they are fluidic revolutionaries sparking a rebellion against inefficiency. They infiltrate the pipelines, overthrowing the mundane and establishing a new order where fluid transfer is a dynamic, autonomous revolution.
6. Enhanced Pumping Technologies:
In the realm of fluid transfer, the heartbeat of efficiency and productivity is embodied by pumping technologies. The evolution of pumping technologies is an ongoing saga of innovation, where each chapter introduces enhancements that redefine the benchmarks of performance, sustainability, and adaptability. Here, we delve into the captivating narrative of Enhanced Pumping Technologies, exploring the groundbreaking trends that promise to reshape the future of fluid handling.
1. Smart Pumping Systems:
The infusion of intelligence into pumping systems heralds the era of Smart Pumping Technologies. These systems leverage sensors and data analytics to optimize pump performance, detect anomalies, and enable predictive maintenance. The result is not just a pump but a cognitive entity that adapts to dynamic operational needs.
2. Variable Frequency Drives (VFDs):
The rise of Variable Frequency Drives represents a paradigm shift in pump control. VFDs allow for precise adjustment of motor speed, matching the pump output to the actual demand. This not only enhances energy efficiency but also extends the lifespan of the pumping system.
3. High-Efficiency Pump Designs:
The relentless pursuit of efficiency has given rise to innovative pump designs that minimize energy losses and maximize fluid transfer. Enhanced impeller designs, streamlined pump casings, and optimized hydraulic profiles collectively contribute to a new standard of high-efficiency pumping.
4. Adaptive and Self-Learning Systems:
Imagine a pump that learns and adapts to its operational environment over time. Adaptive and self-learning pumping systems utilize artificial intelligence and machine learning algorithms to optimize performance based on historical data, fluid characteristics, and system dynamics.
5. Magnetically Driven Pumps:
The advent of magnetically driven pumps eliminates the need for traditional seals, reducing the risk of leaks and enhancing reliability. These pumps use magnetic couplings to transmit torque, ensuring a hermetically sealed system that is particularly valuable in handling corrosive or hazardous fluids.
6. Energy Recovery Systems:
Enhanced pumping technologies embrace sustainability through energy recovery systems. These systems capture and repurpose energy that would otherwise be wasted as heat, contributing to a more energy-efficient and environmentally conscious fluid transfer process.
7. Internet of Things (IoT) Integration:
Pumping technologies are becoming integral components of the Internet of Things (IoT). Connected pumps leverage real-time data exchange for remote monitoring, predictive maintenance, and centralized control. This connectivity ensures a seamless integration of pumping systems into the broader industrial ecosystem.
8. Augmented Reality (AR) for Maintenance:
Maintenance of pumping systems is revolutionized by Augmented Reality. Technicians equipped with AR devices can access real-time information, schematics, and step-by-step instructions overlaid on the physical equipment. This accelerates troubleshooting, reduces downtime, and enhances maintenance efficiency.
9. Nanotechnology in Pump Components:
Nanotechnology infiltrates pump components, introducing materials with enhanced durability, reduced friction, and improved resistance to wear. Nano-coatings on impellers and pump casings contribute to increased efficiency and prolonged component lifespan.
7. Green Fluid Transfer Solutions:
With a growing emphasis on sustainability, fluid transfer technologies will witness a shift towards greener solutions. This includes the use of environmentally friendly fluids, energy-efficient systems, and reduced waste in fluid transfer processes.
8. Advanced Hose and Tubing Materials:
The materials used in hoses and tubing for fluid transfer will evolve to withstand extreme conditions and provide better flexibility. Innovations in materials science will result in hoses that are more durable, resistant to chemicals, and adaptable to various applications.
9. Augmented Reality (AR) for Maintenance:
AR applications will assist technicians in maintenance and repair tasks by providing real-time information, schematics, and guidance during fluid transfer system inspections. This will contribute to faster and more accurate troubleshooting.
10. Digital Twin Technology:
Fluid transfer systems will leverage digital twin technology for virtual modeling and simulation. This will enable engineers to optimize system design, predict performance, and identify potential issues before they arise.
11. Hybrid Fluid Transfer Systems:
Integration of different fluid transfer technologies, such as combining pneumatic and hydraulic systems, will lead to the development of hybrid solutions. These systems will offer improved efficiency and versatility across a range of applications.
12. Energy Recovery Systems:
Future fluid transfer systems will incorporate energy recovery mechanisms to capture and reuse energy during the transfer process. This trend aligns with the broader push towards energy-efficient technologies.
13. Blockchain for Fluid Tracking:
Blockchain technology will be employed to enhance the traceability and transparency of fluid transfer processes. This can be particularly crucial in industries where accurate record-keeping is essential for compliance and quality control.
14. Biocompatible Fluid Transfer in Healthcare:
Advances in fluid transfer technology will be particularly notable in the healthcare sector, with the development of biocompatible materials for fluid transfer systems. This ensures the safe transfer of fluids in medical applications without adverse reactions.
15. Autonomous Fluid Transfer Vehicles:
In industries such as logistics and manufacturing, autonomous vehicles for fluid transfer will become more prevalent. These vehicles will efficiently transport fluids within facilities, optimizing workflow and reducing manual labor.
Conclusion
As we look ahead, the future of fluid transfer technology is characterized by a convergence of smart systems, advanced materials, and sustainable practices. The integration of cutting-edge technologies will not only improve efficiency and reliability but also contribute to a more environmentally conscious and interconnected industrial landscape. Keeping an eye on these trends will be essential for professionals and industries seeking to stay at the forefront of fluid transfer innovation.