Table of Contents
SLS Vs FDM: Which Is Better For 3D Printing in 2024
In the dynamic landscape of additive manufacturing, Selective Laser Sintering (SLS) and Fused Deposition Modeling (FDM) stand out as two prominent 3D printing technologies, each offering unique advantages and applications. As we venture into 2024, the question of which technology reigns supreme for 3D printing continues to intrigue designers, engineers, and manufacturers alike. SLS boasts exceptional material versatility and high precision, while FDM is celebrated for its affordability and ease of use. This comparison delves into the intricacies of SLS versus FDM, exploring their respective strengths and limitations to determine which technology holds the edge in the realm of 3D printing in the year 2024.
What Is SLS 3D Printing?
SLS (Selective Laser Sintering) 3D printing is an additive manufacturing technology that uses a high-powered laser to fuse small particles of powdered material to create a three-dimensional object. In SLS 3D printing, a thin layer of powdered material (typically plastic, metal, or ceramic) is spread evenly across a build platform. Then, a laser selectively fuses the powdered material based on the digital design of the object being created.
The process continues layer by layer, with each layer of powder being fused according to the design until the entire object is formed. One significant advantage of SLS 3D printing is that it does not require support structures, as the surrounding powder acts as a natural support during the printing process. This allows for complex geometries and intricate designs to be produced without the need for additional support removal steps.
What Is FDM 3D Printing?
FDM (Fused Deposition Modeling) 3D printing is an additive manufacturing technology that works by extruding thermoplastic filaments layer by layer to build a three-dimensional object. In FDM printing, a spool of filament is fed into a heated nozzle, where it melts and is deposited onto a build platform according to the digital design of the object being created.
The nozzle moves along the X, Y, and Z axes, depositing the molten material layer by layer until the entire object is formed. As each layer is deposited, it fuses with the previous layer, gradually building up the desired shape.
FDM 3D printing is known for its simplicity, reliability, and affordability compared to other additive manufacturing technologies. It is widely used in various industries and applications, including prototyping, manufacturing tooling, production parts, educational purposes, and hobbyist projects.
Some common thermoplastic materials used in FDM printing include PLA (Polylactic Acid), ABS (Acrylonitrile Butadiene Styrene), PETG (Polyethylene Terephthalate Glycol), and TPU (Thermoplastic Polyurethane), among others. FDM technology allows for the creation of functional prototypes, custom parts, and complex geometries with relatively high accuracy and strength.
What Is 3D Printing?
3D printing, also known as additive manufacturing, is a revolutionary process that creates three-dimensional objects from digital designs. Unlike traditional manufacturing methods that involve subtracting material from a solid block or molding material into a specific shape, 3D printing builds objects layer by layer, adding material where needed. The process begins with the creation of a digital 3D model using computer-aided design (CAD) software or obtained from a 3D scan. This digital model is then sliced into thin horizontal layers, generating a set of instructions (G-code) for the 3D printer. Various types of 3D printing technologies, such as Fused Deposition Modeling (FDM), Stereolithography (SLA), and Selective Laser Sintering (SLS), each with its process and materials, are used to deposit or solidify material layer by layer according to the design. Once printing is complete, post-processing steps like removing support structures, sanding, or painting may be required. 3D printing offers unparalleled advantages including design flexibility, rapid prototyping, customization, and reduced waste, making it a game-changer across industries from aerospace and automotive to healthcare and consumer goods, driving innovation and efficiency to new heights.
FDM 3D Printing Benefits
Fused Deposition Modeling (FDM) 3D printing offers several benefits:
- Cost-Effective: FDM printers are relatively affordable compared to other 3D printing technologies, making them accessible to a wide range of users, including hobbyists, educators, and small businesses.
- Material Variety: FDM printing supports a wide range of thermoplastic materials, including PLA, ABS, PETG, TPU, and more. This variety allows users to choose the material that best suits their specific application, whether it’s for prototyping, functional parts, or concept models.
- Ease of Use: FDM printers are known for their user-friendly operation, making them suitable for beginners and experienced users alike. The printing process typically involves minimal setup and maintenance, allowing users to focus more on their designs and less on technical complexities.
- Support Structures: FDM printing generates support structures automatically when needed, which can be easily removed after printing. This feature enables the creation of complex geometries and overhangs without compromising the integrity of the final object.
- Customization: FDM printing allows for easy customization of designs, whether it’s adjusting size, shape, or features. This flexibility makes it ideal for producing personalized products, prototypes, and one-off creations tailored to specific needs or preferences.
- Rapid Prototyping: With FDM technology, designers and engineers can quickly iterate and test their ideas by producing functional prototypes in-house. This rapid prototyping capability accelerates the product development cycle, reducing time-to-market and overall project costs.
- Low Waste: FDM printing generates minimal waste compared to traditional manufacturing methods, as it only uses the amount of material required to build the object. Additionally, some FDM filaments are biodegradable or recyclable, further reducing environmental impact.
SLS 3D Printing Benefits
Selective Laser Sintering (SLS) 3D printing offers several benefits:
- Material Versatility: SLS can utilize a wide range of materials, including various polymers, metals, and ceramics. This versatility allows for the production of parts with different mechanical, thermal, and chemical properties, suitable for diverse applications across industries.
- High Accuracy and Resolution: SLS technology enables the creation of highly detailed and precise parts with intricate geometries. The laser selectively sinters the powdered material, resulting in smooth surfaces and fine features, making it ideal for producing complex prototypes and end-use parts.
- No Need for Support Structures: Unlike some other 3D printing processes, SLS does not require support structures to hold up overhanging features during printing. This eliminates the need for post-processing to remove supports, saving time and material.
- Material Recycling: SLS printing typically uses powdered material as the raw feedstock and any unused powder can be recycled and reused for subsequent prints. This recycling capability reduces material waste and contributes to cost savings over time.
- Production of Functional Parts: SLS-produced parts exhibit excellent mechanical properties, including strength, durability, and heat resistance. This makes them suitable for producing functional prototypes, end-use parts, and components for demanding applications in industries such as aerospace, automotive, and healthcare.
- Design Freedom: SLS technology allows designers to create complex shapes and intricate designs that would be difficult or impossible to achieve using traditional manufacturing methods. This design freedom enables innovation and optimization of product performance while minimizing material usage.
- Fast Turnaround Times: SLS 3D printing offers relatively fast turnaround times compared to traditional manufacturing processes. Once the digital design is finalized, parts can be printed in a matter of hours or days, depending on their size and complexity, facilitating rapid prototyping and production.
SLS Vs FDM 3D Printing
Selective Laser Sintering (SLS) and Fused Deposition Modeling (FDM) are two popular 3D printing technologies, each with its advantages and limitations. Here’s a comparison between SLS and FDM:
Technology:
- SLS: SLS uses a high-powered laser to selectively sinter powdered material, such as plastic, metal, or ceramic, layer by layer to build the object.
- FDM: FDM extrudes thermoplastic filament through a heated nozzle onto a build platform, layer by layer, to create the object.
Material Selection:
- SLS: SLS supports a wider range of materials, including various polymers, metals, and ceramics.
- FDM: FDM primarily uses thermoplastic materials such as PLA, ABS, PETG, and TPU, though some metal-filled filaments are available.
Surface Finish:
- SLS: SLS typically produces smoother surface finishes with finer details due to the powder-based process.
- FDM: FDM parts may have visible layer lines and rougher surface finishes compared to SLS.
Accuracy and Resolution:
- SLS: SLS generally offers higher accuracy and resolution, making it suitable for producing intricate and detailed parts.
- FDM: FDM parts can have lower accuracy and resolution, particularly with complex geometries or small features.
Support Structures:
- SLS: SLS does not require support structures because unsintered powder acts as self-supporting during printing.
- FDM: FDM often requires support structures for overhangs and complex geometries, which need to be removed after printing.
Material Recycling:
- SLS: Unused powder in SLS can be recycled and reused for subsequent prints, reducing material waste.
- FDM: FDM produces less waste compared to traditional manufacturing methods but does not offer as straightforward a recycling process as SLS.
Applications:
- SLS: SLS is well-suited for producing functional prototypes, end-use parts, and components with high mechanical properties, often used in aerospace, automotive, and medical industries.
- FDM: FDM is widely used for rapid prototyping, concept modeling, educational purposes, and producing low-cost, low-volume parts across various industries.
A Key Difference Between SLS and FDM 3D Printing
The key differences between SLS (Selective Laser Sintering) and FDM (Fused Deposition Modeling) 3D printing are as follows:
Technology:
- SLS: Utilizes a high-powered laser to selectively sinter powdered material layer by layer, bonding it together to form the object.
- FDM: Extrudes thermoplastic filament through a heated nozzle onto a build platform, layer by layer, to create the object.
-
Materials:
- SLS: Supports a wide range of materials including various polymers, metals, and ceramics.
- FDM: Primarily uses thermoplastic materials such as PLA, ABS, PETG, and TPU, with fewer options for metals and ceramics.
-
Surface Finish:
- SLS: Typically produces smoother surface finishes with finer details due to the powder-based process.
- FDM: Parts may have visible layer lines and rougher surface finishes compared to SLS.
-
Accuracy and Resolution:
- SLS: Generally offers higher accuracy and resolution, making it suitable for producing intricate and detailed parts.
- FDM: Parts can have lower accuracy and resolution, particularly with complex geometries or small features.
-
Support Structures:
- SLS: Does not require support structures because unsintered powder acts as self-supporting during printing.
- FDM: Often requires support structures for overhangs and complex geometries, which need to be removed after printing.
-
Material Recycling:
- SLS: Unused powder can be recycled and reused for subsequent prints, reducing material waste.
- FDM: Produces less waste compared to traditional manufacturing methods but does not offer as straightforward a recycling process as SLS.
-
Applications:
- SLS: Well-suited for producing functional prototypes, end-use parts, and components with high mechanical properties, often used in aerospace, automotive, and medical industries.
- FDM: Widely used for rapid prototyping, concept modeling, educational purposes, and producing low-cost, low-volume parts across various industries.
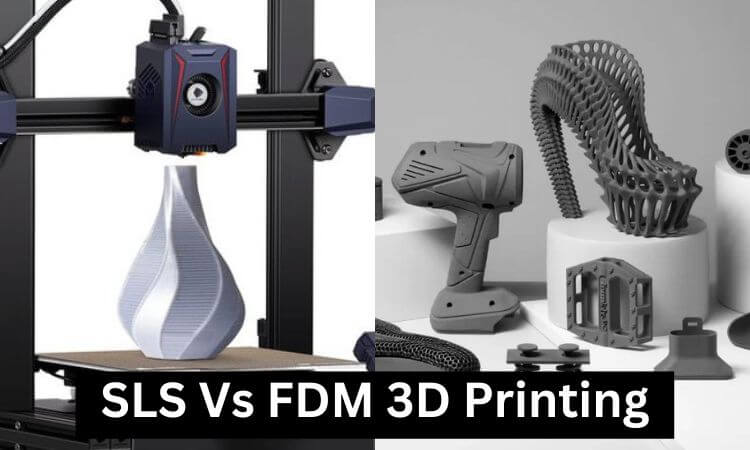
SLS Vs FDM: Which Is Better For 3D Printing
Determining whether SLS (Selective Laser Sintering) or FDM (Fused Deposition Modeling) is better for 3D printing depends on various factors, including the specific requirements of your project, budget considerations, material options, surface finish needs, and intended applications. Each technology has its strengths and limitations, so the “better” option will depend on your circumstances. Here’s a comparison to help you decide:
Choose SLS if:
- Material Versatility: You require a wide range of material options, including polymers, metals, and ceramics.
- High Accuracy and Resolution: Your project demands high precision and intricate details.
- Complex Geometries: You need to produce parts with complex geometries without the need for support structures.
- Functional Prototypes or End-Use Parts: You’re producing functional prototypes or end-use parts that require excellent mechanical properties and durability.
- No Post-Processing Required: You prefer minimal post-processing, as SLS parts typically have smoother surface finishes.
Choose FDM if:
- Cost-Effectiveness: You’re working within a limited budget, as FDM printers are generally more affordable than SLS machines.
- Material Availability: You primarily require thermoplastic materials such as PLA, ABS, PETG, or TPU, with fewer needs for metals or ceramics.
- Rapid Prototyping: You need quick turnaround times for prototyping and iterative design processes.
- Educational or Hobbyist Projects: You’re engaging in educational or hobbyist projects where ease of use and accessibility are important factors.
- Low to Medium Complexity Parts: Your parts have relatively simple geometries and do not require extremely high precision or surface finish.
Ultimately, the “better” option depends on your specific project requirements, budget, timeline, and desired outcomes. Both SLS and FDM have their strengths and are valuable tools in the realm of 3D printing, serving different purposes and catering to different needs.
What is 3D printing?
3D printing, also known as additive manufacturing, is a process of creating three-dimensional objects from digital designs by adding material layer by layer.
How does 3D printing work?
3D printing works by slicing a digital model into thin horizontal layers, then depositing or solidifying material layer by layer according to the design, typically using a 3D printer.
What materials can be used in 3D printing?
3D printing materials vary depending on the printing technology but commonly include thermoplastics (e.g., PLA, ABS), metals, ceramics, resins, and composites.
What are the different types of 3D printing technologies?
Some common 3D printing technologies include Fused Deposition Modeling (FDM), Stereolithography (SLA), Selective Laser Sintering (SLS), Direct Metal Laser Sintering (DMLS), and Binder Jetting, among others.
What are the applications of 3D printing?
3D printing has various applications across industries, including prototyping, product development, manufacturing tooling, custom parts production, healthcare (e.g., medical implants, prosthetics), aerospace, automotive, architecture, and education.
What are the advantages of 3D printing?
Key advantages of 3D printing include design flexibility, rapid prototyping, customization, reduced waste, cost-effectiveness for low-volume production, and the ability to create complex geometries and intricate designs.
What are the limitations of 3D printing?
Limitations of 3D printing include slower production speeds compared to traditional manufacturing methods for mass production, limited material choices for some printing technologies, post-processing requirements, and challenges with achieving certain surface finishes and mechanical properties.
Is 3D printing suitable for mass production?
While 3D printing is excellent for rapid prototyping and low-volume production, it may not be as cost-effective or efficient as traditional manufacturing methods for large-scale mass production due to slower production speeds and material costs.
What software is used for creating 3D models for printing?
Various computer-aided design (CAD) software tools are used for creating 3D models for printing, including Autodesk Fusion 360, SolidWorks, Tinkercad, Blender, and others.
How do I get started with 3D printing?
To get started with 3D printing, you’ll need a 3D printer, digital 3D models (which you can create or download), slicing software to prepare models for printing, and filament or resin suitable for your printer’s technology. Additionally, learning resources such as tutorials, online communities, and forums can help you get started and improve your skills.
Conclusion:
In the ever-evolving landscape of additive manufacturing, the choice between Selective Laser Sintering (SLS) and Fused Deposition Modeling (FDM) remains nuanced and dependent on specific project requirements. As we conclude our exploration into the realm of 3D printing in 2024, it becomes evident that neither technology holds an absolute advantage over the other. Instead, the decision between SLS and FDM hinges on factors such as material selection, surface finish needs, budget considerations, and intended applications. Whether one prioritizes the high precision of SLS or the cost-effectiveness of FDM, both technologies continue to drive innovation and transformation across industries, ushering in a new era of manufacturing possibilities. Ultimately, the true measure of success lies in leveraging the strengths of each technology to achieve optimal outcomes in the ever-expanding landscape of additive manufacturing.